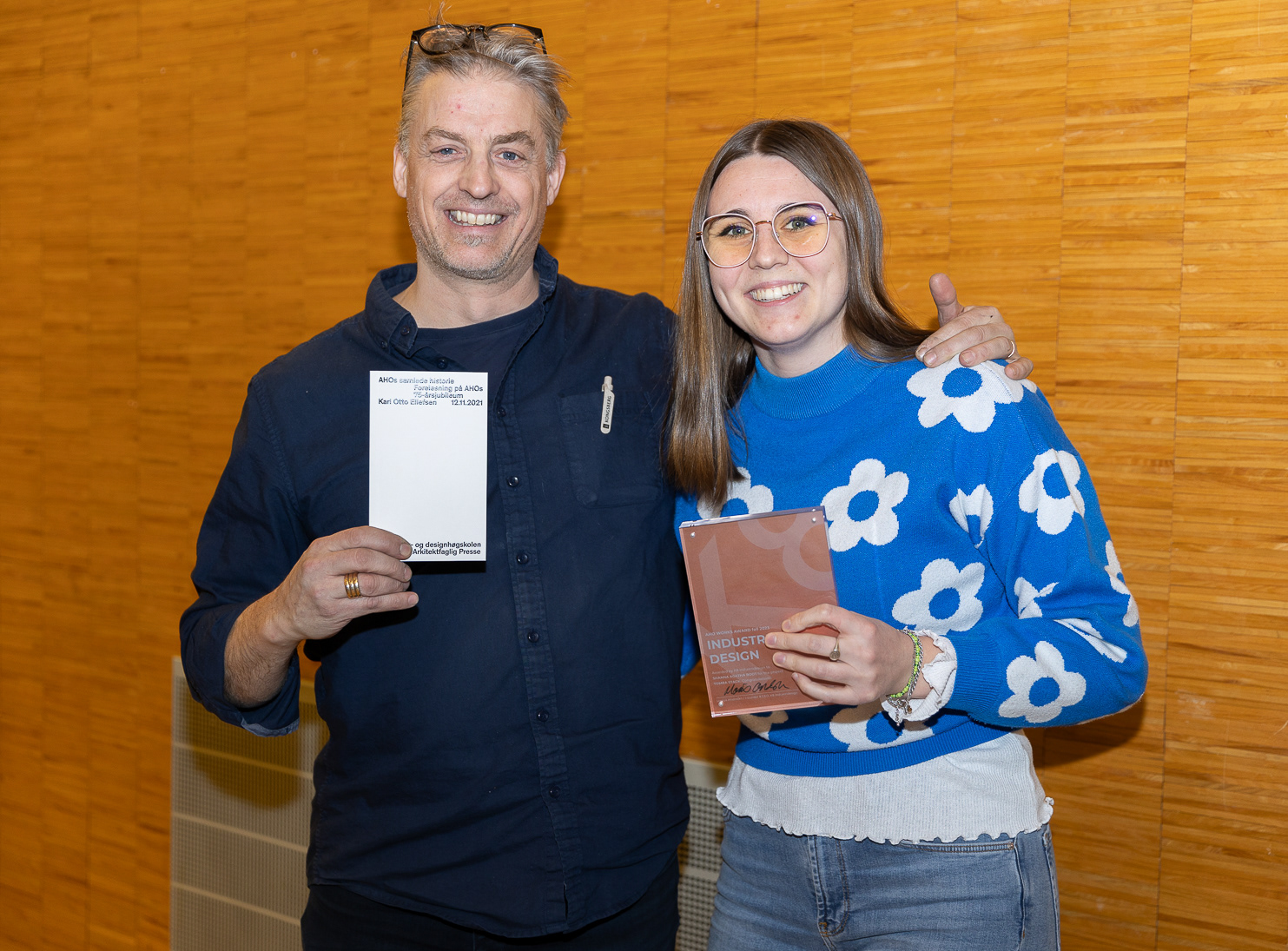
K8 the jury of the AHOW WORKS AWARD for Industrial Design Autumn 2023 said the following about me and the design
"The student has taken upon a complex task with multiple layers. Shanna has re-designed reverse vending machine modules for recycling bottles and cans. Her design solution is calculated and holistic-tapping into multiple design challenges, such as transport volume, ergonomics, and material usage.
We find it especially interesting to see this type of product, which is rarely addressed by students, but more than consumer products. It is truly inspiring to see a young designer digging into the *ugly and boring backside* of a system with enthusiasm.
Despite being a technical product, the student has paid attention to ergonomics, user interaction, and brand aesthetics- which are core design values that any product and user deserves to have addressed.
On top of this, we are thrilled to see that the student has designed with rational use of material and low volume during transport. Addressing such matters conveys the students' deeper understanding of construction principles and manufacturing processes. These skills and practices are essential to create a more sustainable product design."
A short insight of my design journey (in pictures).
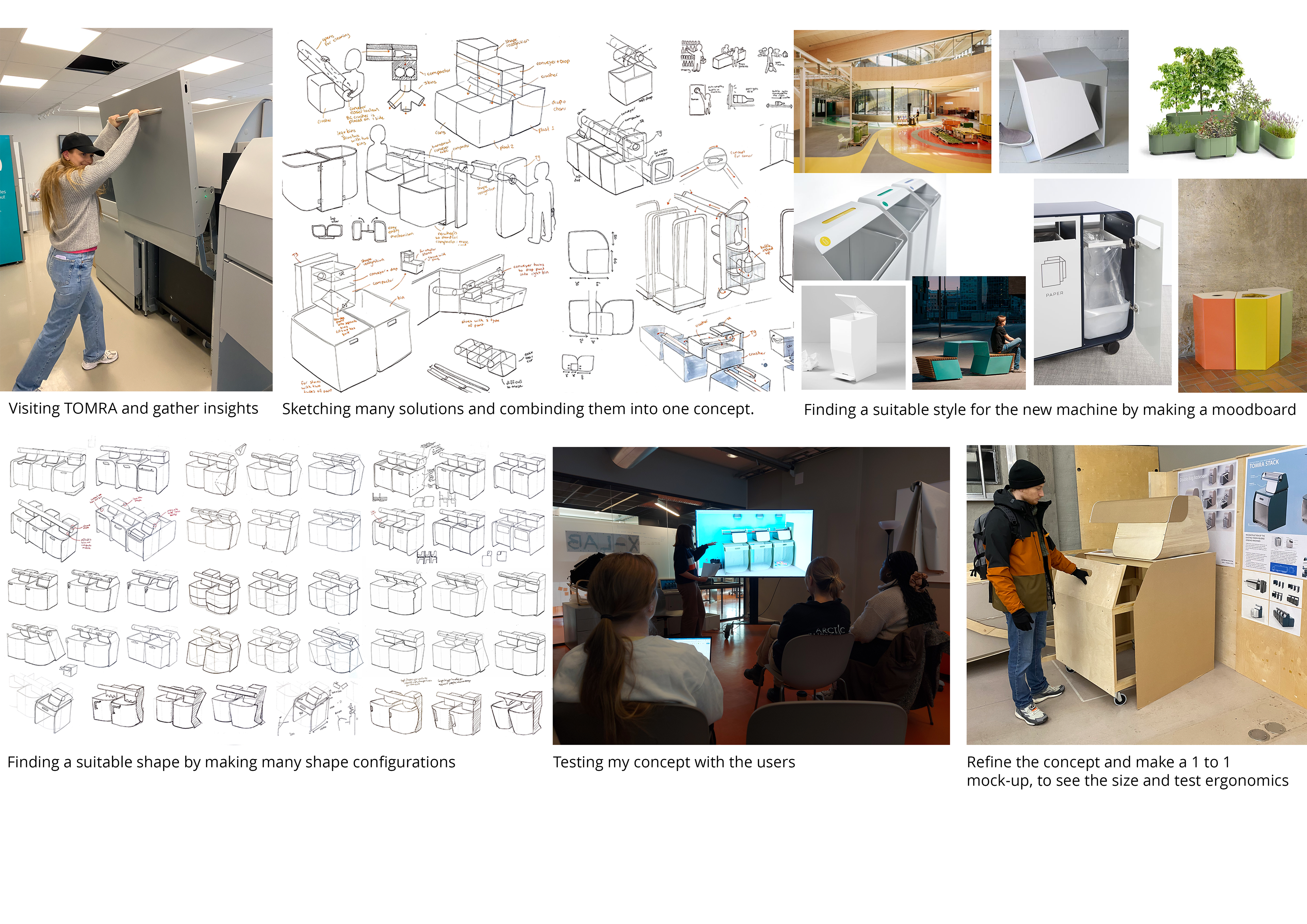
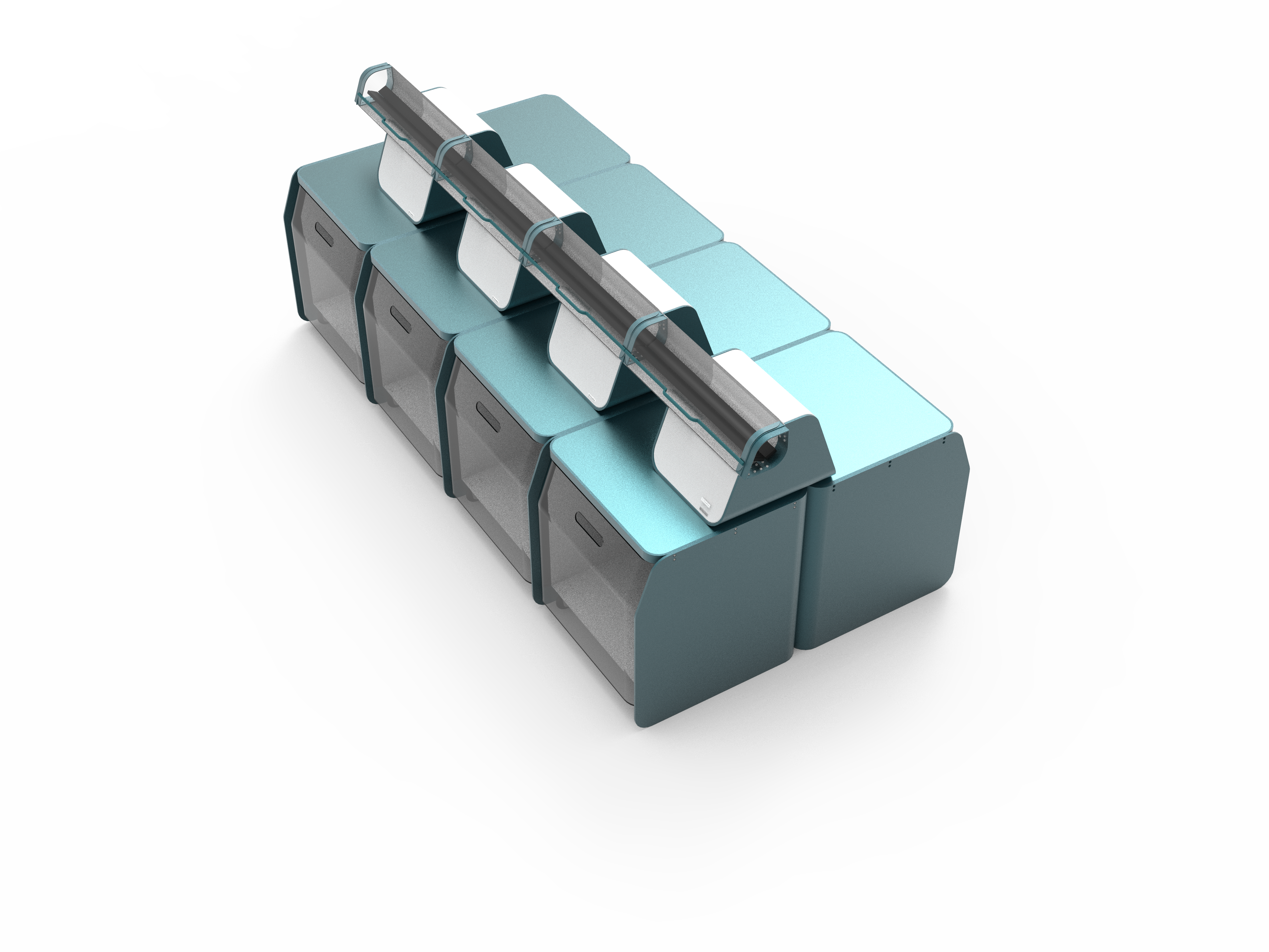
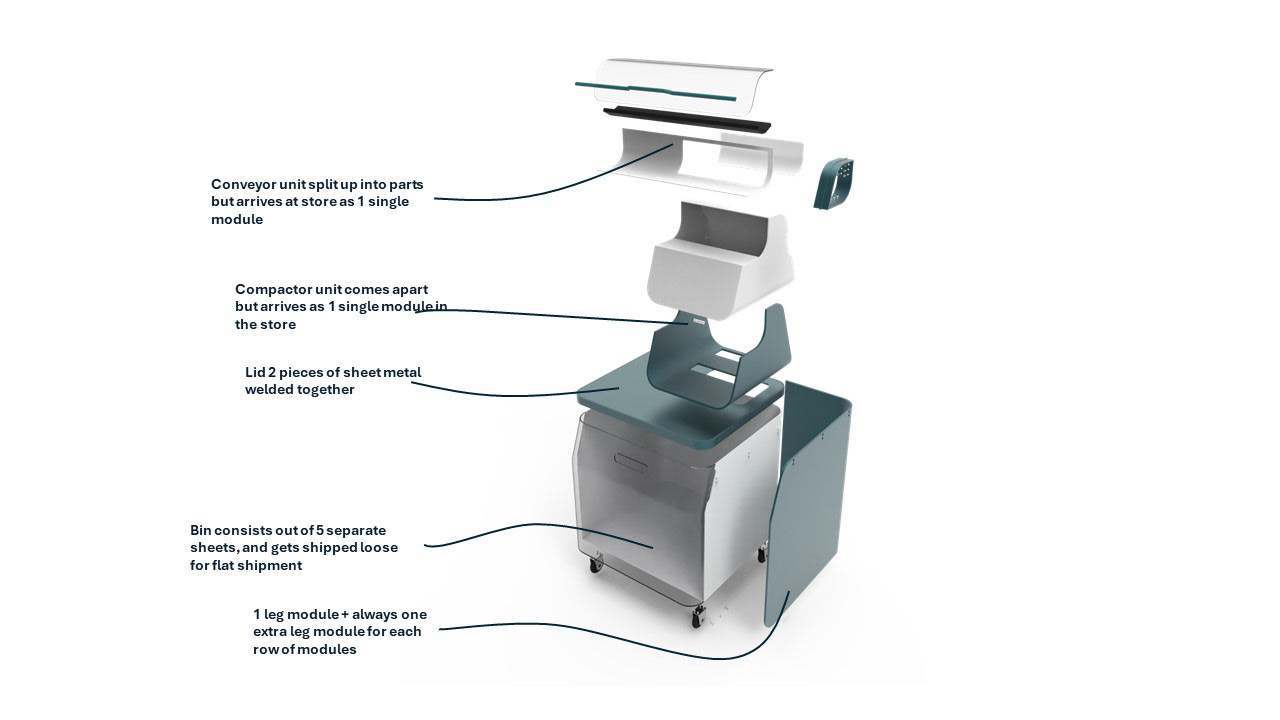
Tomra faces a challenge in achieving their expansion goals due to limitations with their existing machines, which were not designed to be easily scaled up to meet the growing demand. The complexity and size of their enormous machines poses a significant obstacle, particularly when customers can customize various parts. Tomra can only start production once all customer preferences are known, resulting in a fully tailored machine, a process that typically takes a year.
After consulting experts at Tomra and engaging with users ,that have experience working with these machines, through workshops, I discovered that a modular approach was the optimal solution. Because if a new modular machine needs to be build Tomra needs to do an entire re design of the current machine, this means other issues with the current machine can also be addressed such as including improvements in ergonomics for store personnel, enhanced usability, reduced material usage, and minimized transport volume.
In my effort to create a more efficient solution, I made the Tomra modules more appealing to companies seeking to expand their cans and bottle storage. Unlike the current machines that require the purchase of an entire new system for compaction and scanning, my innovative TOMRA Stack concept simplifies the process by only having to buy a new container. This not only reduces costs but also contributes to a more sustainable approach.
The TOMRA Stack concept is meant to assist Tomra in realizing its expansion plan, simplifying scalability by minimizing the need for extensive customization without compromising the essence of tailoring for customers. With the ability to build stock, Tomra can now deliver machines to customers more promptly. The transparent nature of the TOMRA Stack is particularly advantageous for new store workers, providing a clear understanding of its functionality. Additionally, the overall friendlier design language creates a positive atmosphere in the backroom, making it a pleasant and efficient work environment.
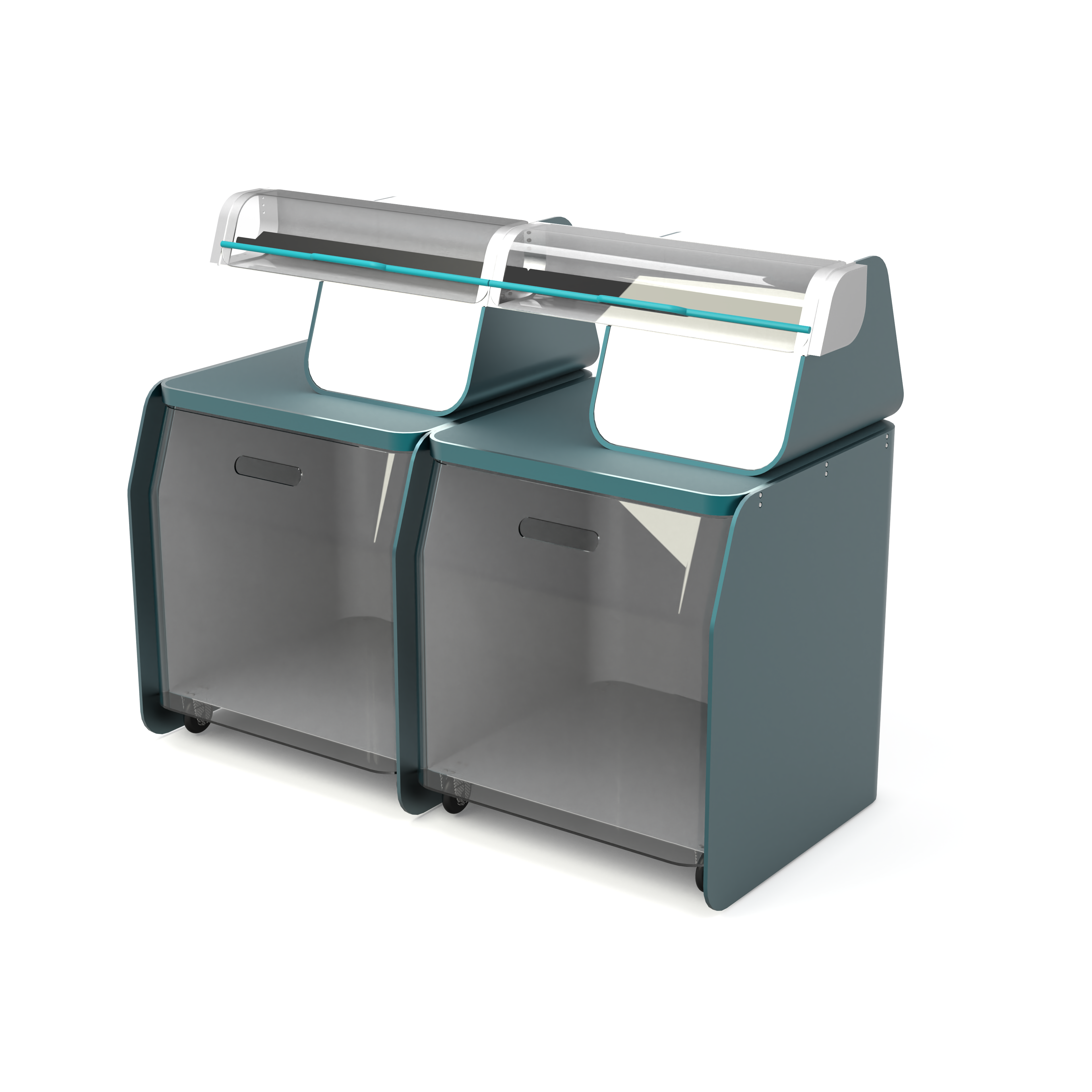
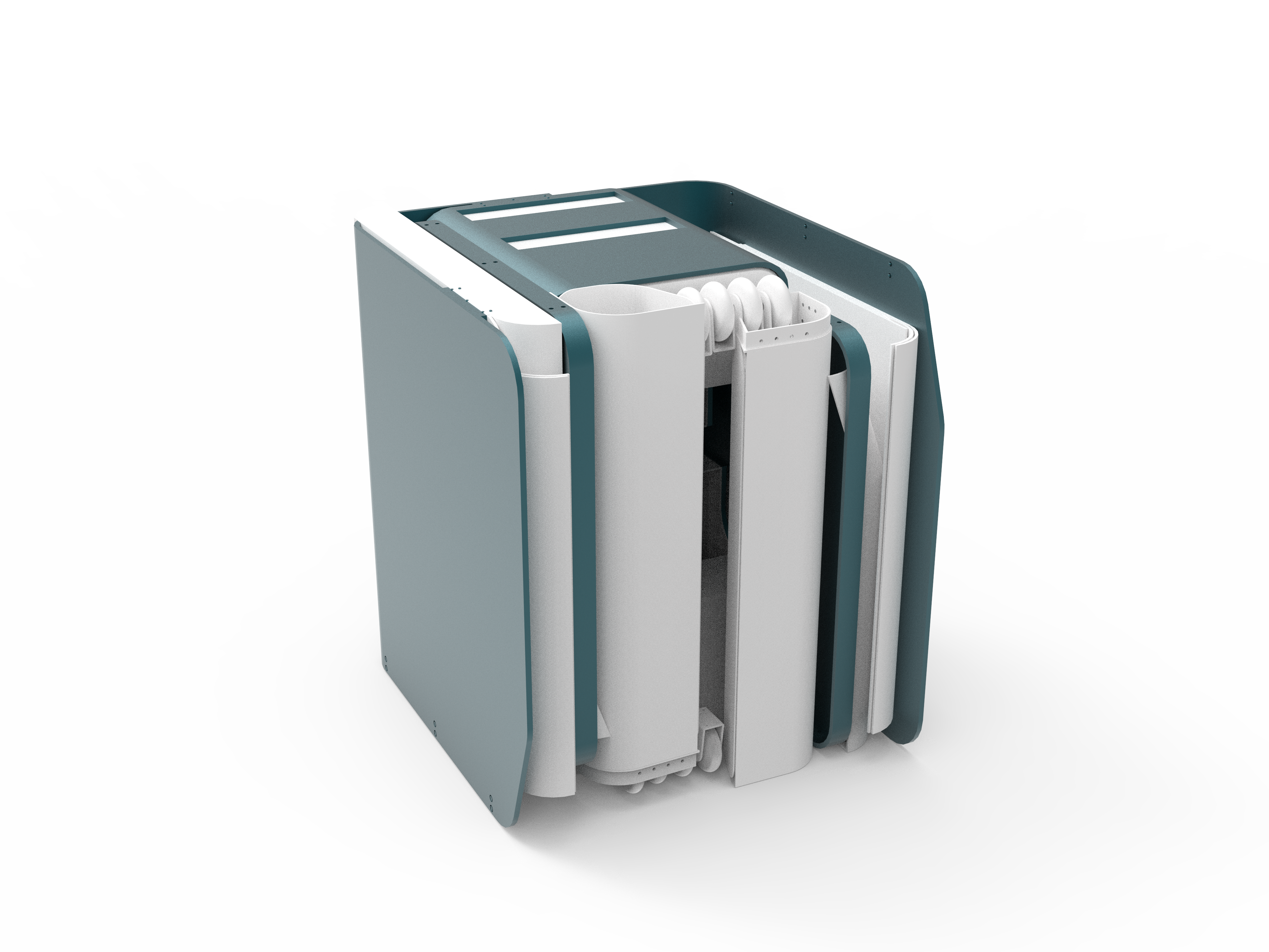